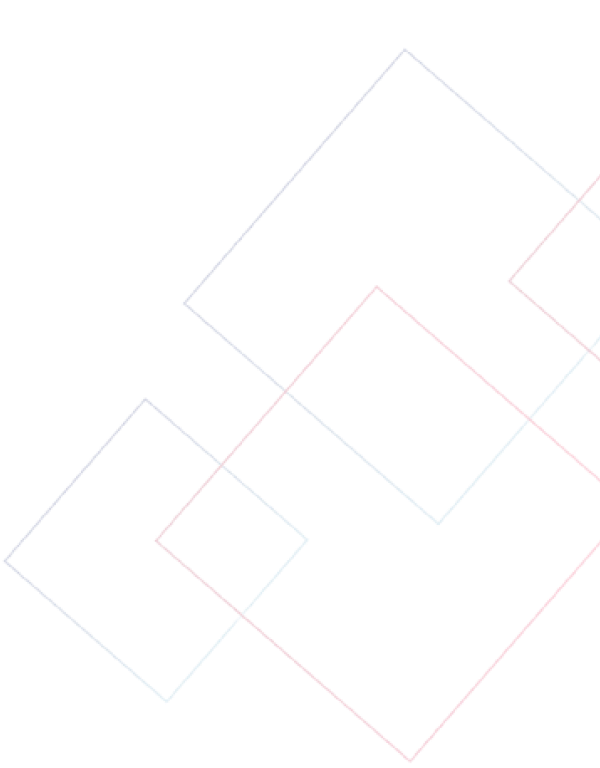
卧式丁基胶涂布机传动系统维护要点解析
时间:2025-05-20 来源:http://www.jncsjx.com/ 发布人:昌盛机械
在软包装生产领域,卧式丁基胶涂布机凭借其高精度涂布能力,成为光伏组件、建筑密封等行业的核心设备。其传动系统作为设备运行的“神经中枢”,直接决定涂布均匀性、生产效率及运行稳定性。本文将从技术原理与工程实践双维度,系统性阐述传动系统的维护要点,为行业提供兼具理论深度与实用价值的操作指南。
In the field of flexible packaging production, the horizontal butyl rubber coating machine has become a core equipment in industries such as photovoltaic modules and building sealing due to its high-precision coating capability. The transmission system, as the "nerve center" of equipment operation, directly determines the uniformity of coating, production efficiency, and operational stability. This article will systematically explain the maintenance points of the transmission system from both technical principles and engineering practice, providing the industry with a practical and theoretical operation guide.
一、传动系统技术架构解析
1、 Analysis of Transmission System Technical Architecture
卧式丁基胶涂布机传动系统由伺服电机、行星减速机、同步带轮、张紧装置及涂布辊组成。其核心功能是实现胶料输送速度与涂布辊转速的精准匹配,确保胶层厚度偏差控制在±2μm以内。系统工作原理如下:
The transmission system of the horizontal butyl rubber coating machine consists of a servo motor, planetary reducer, synchronous belt pulley, tensioning device, and coating roller. Its core function is to achieve precise matching between the conveying speed of the adhesive material and the speed of the coating roller, ensuring that the thickness deviation of the adhesive layer is controlled within ± 2 μ m. The working principle of the system is as follows:
动力传输路径:伺服电机输出扭矩经行星减速机放大后,通过同步带传递至涂布辊。张紧装置动态调节皮带张力,防止打滑现象。
Power transmission path: The output torque of the servo motor is amplified by the planetary reducer and transmitted to the coating roller through the synchronous belt. The tensioning device dynamically adjusts the belt tension to prevent slipping.
速度闭环控制:编码器实时采集涂布辊转速,与设定值比对后,由伺服驱动器调整电机输出,形成全数字闭环控制系统。
Speed closed-loop control: The encoder real-time collects the speed of the coating roller, compares it with the set value, and adjusts the motor output by the servo driver to form a fully digital closed-loop control system.
负载均衡机制:双辊传动结构采用刚性联轴器连接,通过预紧力调节装置,确保两辊线速度差值小于0.5%。
Load balancing mechanism: The dual roller transmission structure is connected by a rigid coupling, and the pre tension adjustment device is used to ensure that the difference in linear velocity between the two rollers is less than 0.5%.
二、关键部件维护策略
2、 Key component maintenance strategy
1. 同步带维护
1. Synchronous belt maintenance
张力动态管理:采用激光对中仪检测皮带跨距,通过张紧轮螺栓调节预紧力。建议每周使用皮带张力计校准,确保张力值在标准值的±5%范围内。
Dynamic tension management: Laser centering instrument is used to detect the belt span, and the pre tension force is adjusted through the tensioning wheel bolt. It is recommended to calibrate the belt tension meter weekly to ensure that the tension value is within ± 5% of the standard value.
磨损监测技术:在皮带侧面设置磨损标记线,当标记线消失时,表明皮带齿高磨损超过20%,需立即更换。同步带轮齿面应保持清洁,避免胶料残留导致异常磨损。
Wear monitoring technology: Set wear marking lines on the side of the belt. When the marking lines disappear, it indicates that the belt teeth have worn more than 20% and need to be replaced immediately. The tooth surface of the synchronous belt should be kept clean to avoid abnormal wear caused by residual rubber material.
2. 轴承润滑管理
2. Bearing lubrication management
润滑剂选型:根据工况温度选择润滑脂,常温环境(20℃-40℃)采用NLGI 2级锂基脂,高温环境(>60℃)升级为复合磺酸钙基脂。
Lubricant selection: Choose lubricating grease according to the operating temperature. For normal temperature environments (20 ℃ -40 ℃), use NLGI grade 2 lithium based grease, and upgrade to composite calcium sulfonate based grease for high temperature environments (>60 ℃).
智能润滑系统:配置单点润滑器,设置3个月为润滑周期。对于重载轴承,采用油气润滑装置,通过脉冲式供油确保润滑膜完整。
Intelligent lubrication system: equipped with a single point lubricator and set a lubrication cycle of 3 months. For heavy-duty bearings, an oil air lubrication device is used to ensure the integrity of the lubrication film through pulsed oil supply.
3. 减速机维护
3. Maintenance of gearbox
油液监控方案:每季度取样检测油液粘度、水分及金属颗粒含量。当运动粘度变化超过15%,或水分含量超过0.1%,立即更换润滑油。
Oil monitoring plan: Sampling and testing of oil viscosity, moisture, and metal particle content every quarter. When the viscosity changes by more than 15% or the moisture content exceeds 0.1%, immediately replace the lubricating oil.
密封件检查:每月检查输入输出轴密封圈,采用荧光检漏剂探测微小渗漏。发现油渍时,需在8小时内更换骨架油封。
Seal inspection: Check the input and output shaft sealing rings monthly and use fluorescent leak detectors to detect minor leaks. When oil stains are found, the skeleton oil seal needs to be replaced within 8 hours.
三、精密对中调整技术
3、 Precision alignment and adjustment technology
1. 激光对中工艺
1. Laser alignment process
三维校准法:使用激光对中仪,在减速机与电机法兰盘投影面设置三个测量点。通过调整电机底脚螺栓,使同心度偏差≤0.02mm,角度偏差≤0.05mm/m。
Three dimensional calibration method: Use a laser alignment instrument to set three measurement points on the projection surface of the reducer and motor flange. Adjust the motor foot bolts to ensure concentricity deviation ≤ 0.02mm and angle deviation ≤ 0.05mm/m.
动态补偿机制:在设备空载运行状态下,再次进行对中校准,补偿热膨胀引起的位移偏差。实测表明,该技术可使传动效率提升8%。
Dynamic compensation mechanism: During the no-load operation of the equipment, perform centering calibration again to compensate for displacement deviation caused by thermal expansion. Tests have shown that this technology can increase transmission efficiency by 8%.
2. 联轴器预紧力控制
2. Pre tightening force control of coupling
扭矩扳手应用:采用数字式扭矩扳手,按联轴器规格设定预紧扭矩。对于梅花形联轴器,预紧扭矩值控制在额定扭矩的1.2-1.5倍。
Application of torque wrench: Using a digital torque wrench, set the pre tightening torque according to the specifications of the coupling. For the plum blossom shaped coupling, the pre tightening torque value should be controlled at 1.2-1.5 times the rated torque.
防松设计:在螺栓螺纹处涂抹螺纹锁固剂,配合弹簧垫圈使用。每半年检查螺栓伸长量,当伸长量超过0.05mm时,需重新紧固。
Anti loosening design: Apply thread locking agent to the bolt threads and use it in conjunction with spring washers. Check the elongation of bolts every six months. If the elongation exceeds 0.05mm, it needs to be re tightened.
四、智能监测系统部署
4、 Deployment of Intelligent Monitoring System
1. 振动分析技术
1. Vibration analysis technology
在线监测模块:在电机、减速机、轴承座安装三向加速度传感器,实时采集振动信号。通过FFT频谱分析,识别齿轮啮合频率、轴承故障特征频率。
Online monitoring module: Install three-way acceleration sensors on the motor, reducer, and bearing seat to collect real-time vibration signals. Identify gear meshing frequency and bearing fault characteristic frequency through FFT spectrum analysis.
预警阈值设定:建立设备振动数据库,当振动速度有效值超过基准值30%时,触发黄色预警;超过50%时,启动红色警报并停机检修。
Warning threshold setting: Establish a device vibration database, and trigger a yellow warning when the effective value of vibration speed exceeds 30% of the reference value; When it exceeds 50%, activate a red alarm and shut down for maintenance.
2. 温度巡检系统
2. Temperature inspection system
红外测温网络:在传动部件表面布置红外测温探头,形成温度场分布图。设置三级温度报警:一级80℃,二级90℃,三级100℃。
Infrared temperature measurement network: Install infrared temperature measurement probes on the surface of transmission components to form a temperature field distribution map. Set up a three-level temperature alarm: Level 1 at 80 ℃, Level 2 at 90 ℃, and Level 3 at 100 ℃.
热成像诊断:每季度使用热成像仪进行全面扫描,建立温度云图档案。异常温升区域需在48小时内完成拆检。
Thermal imaging diagnosis: Use a thermal imaging device to conduct comprehensive scans every quarter and establish a temperature cloud map file. The area with abnormal temperature rise needs to be dismantled and inspected within 48 hours.
五、维护周期优化方案
5、 Maintenance cycle optimization plan
1. 状态监测维护(CBM)
1. Condition Monitoring and Maintenance (CBM)
数据驱动决策:基于振动、温度、油液分析数据,动态调整维护周期。对于运行平稳的设备,可延长定期维护间隔至6个月。
Data driven decision-making: Based on vibration, temperature, and oil analysis data, dynamically adjust maintenance cycles. For equipment that runs smoothly, the regular maintenance interval can be extended to 6 months.
备件智能管理:建立关键部件寿命模型,预测轴承、皮带等易损件剩余寿命。当预测值低于20%时,自动生成备件采购申请。
Intelligent spare parts management: Establish a key component life model to predict the remaining life of vulnerable parts such as bearings and belts. When the predicted value is below 20%, a spare parts procurement request will be automatically generated.
2. 预防性维护(PM)
2. Preventive Maintenance (PM)
润滑周期优化:根据环境湿度、粉尘浓度调整润滑频率。在洁净车间(ISO 7级),润滑周期可延长至6个月。
Lubrication cycle optimization: Adjust the lubrication frequency according to environmental humidity and dust concentration. In the clean room (ISO 7 level), the lubrication cycle can be extended to 6 months.
清洁度控制:每日生产结束后,用异丙醇擦拭传动部件表面。每季度进行深度清洁,使用高压气枪清除内部积尘。
Cleanliness control: After daily production, wipe the surface of transmission components with isopropanol. Perform deep cleaning every quarter and use high-pressure air guns to remove internal dust accumulation.
通过实施上述维护策略,可使卧式丁基胶涂布机传动系统的无故障运行时间延长至8000小时以上,涂布精度稳定性提升30%,为连续化生产提供坚实保障。
By implementing the above maintenance strategy, the fault free operation time of the transmission system of the horizontal butyl rubber coating machine can be extended to over 8000 hours, and the stability of coating accuracy can be improved by 30%, providing a solid guarantee for continuous production.
本文由卧式丁基胶涂布机友情奉献.更多有关的知识请点击:http://www.jncsjx.com我们将会对您提出的疑问进行详细的解答,欢迎您登录网站留言.
This article is a friendly contribution from glass coating machine equipment For more information, please click: http://www.jncsjx.com We will provide detailed answers to your questions. You are welcome to log in to our website and leave a message
- 双组份打胶机详解:从设计到使用维护 2025/07/30
- 双组份打胶机:应用领域与核心优势 2025/07/28
- 卧式丁基胶涂布机:选型需考量这些方面 2025/07/25
- 全自动封胶线使用注意事项:保障高效稳定运行的关键要点 2025/07/24
- 双组份打胶机怎么用?使用方法解析 2025/07/23
- 全自动封胶线胶线的关键特性与应用要点 2025/07/22
- 中空玻璃加工设备的组成解析:从切割到密封 2025/07/21
- 全自动封胶线是什么的相关介绍 2025/07/18
- 中空玻璃加工设备主要类型及用途 2025/07/16
- 卧式丁基胶涂布机操作技术规范 2025/07/14