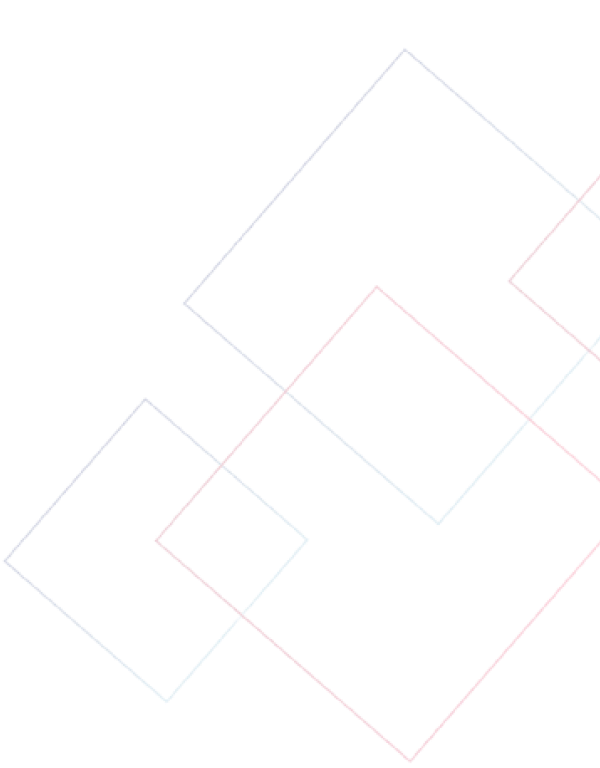
全自动封胶线使用注意事项:保障高效稳定运行的关键要点
时间:2025-07-24 来源:http://www.jncsjx.com/ 发布人:昌盛机械
全自动封胶线作为实现密封胶均匀涂布的自动化设备,广泛应用于建材、汽车零部件、电子元件等领域的密封工序,其运行状态直接影响产品密封性能(如防水、防尘、防漏)与生产效率。使用过程中需兼顾设备特性、胶料性能与操作规范,通过科学管理规避常见问题(如胶线断胶、气泡、尺寸偏差),确保封胶合格率稳定在 99% 以上,同时延长设备使用寿命(通常可达 5-8 年)。
As an automated equipment for achieving uniform application of sealant, the fully automatic sealing line is widely used in sealing processes in the fields of building materials, automotive parts, electronic components, etc. Its operating status directly affects the sealing performance (such as waterproof, dustproof, leak proof) and production efficiency of the product. During use, it is necessary to consider the characteristics of the equipment, the performance of the rubber material, and the operating standards. Common problems such as broken rubber lines, bubbles, and dimensional deviations should be avoided through scientific management to ensure a stable sealing qualification rate of over 99%, while extending the service life of the equipment (usually up to 5-8 years).
设备启动前的准备工作是保障运行的基础,需覆盖参数核查与状态确认。首先检查胶料状态:密封胶需提前预热至 25-35℃(粘度控制在 5000-15000mPas,根据胶种调整),避免因温度过低导致流动性差(出现胶线断续)或过高导致胶料变质(适用期缩短)。胶料桶需密封良好(防止空气进入产生气泡),并通过滤网(精度 50-100 目)过滤杂质(杂质会堵塞胶嘴,造成涂布不均)。其次校准设备参数:根据产品尺寸设定胶嘴移动速度(10-50mm/s)、胶量输出(0.5-5ml/s)、胶线宽度(2-10mm),并通过试涂确认胶线位置偏差(≤±0.5mm),必要时调整机械定位(如导轨平行度、胶嘴高度)。最后检查辅助系统:压缩空气压力需稳定在 0.4-0.6MPa(压力波动≤±0.02MPa),否则会导致胶量忽大忽小;加热装置(如胶管加热带)需提前启动,确保胶料在输送过程中温度恒定(偏差≤±2℃)。
The preparation work before equipment startup is the foundation for ensuring operation, which needs to cover parameter verification and status confirmation. Firstly, check the condition of the adhesive material: the sealant needs to be preheated to 25-35 ℃ in advance (viscosity controlled at 5000-15000mPas, adjusted according to the type of adhesive) to avoid poor fluidity (intermittent adhesive lines) caused by low temperature or deterioration of the adhesive material (shortened shelf life) caused by high temperature. The glue bucket needs to be well sealed (to prevent air from entering and generating bubbles), and impurities should be filtered through a filter (with an accuracy of 50-100 mesh) (impurities can clog the glue nozzle and cause uneven coating). Next, calibrate the equipment parameters: set the nozzle movement speed (10-50mm/s), adhesive output (0.5-5ml/s), and adhesive line width (2-10mm) according to the product size, and confirm the adhesive line position deviation (≤± 0.5mm) through trial coating. If necessary, adjust the mechanical positioning (such as rail parallelism and nozzle height). Finally, check the auxiliary system: the compressed air pressure needs to be stable at 0.4-0.6MPa (pressure fluctuation ≤± 0.02MPa), otherwise it will cause the glue volume to fluctuate between large and small; Heating devices (such as rubber hose heating belts) need to be started in advance to ensure a constant temperature of the rubber material during transportation (deviation ≤± 2 ℃).
运行过程中的实时监控与调整是保证封胶质量的核心。操作人员需持续观察胶线外观:正常胶线应连续光滑、无气泡、无缺胶,若出现气泡(混入空气),需停机排出胶管内空气;若胶线变细(胶量不足),检查胶泵压力是否下降(需维持在 0.8-1.5MPa);若出现毛边(胶嘴磨损),及时更换胶嘴(更换时间<5 分钟)。设备运行时需避免急停急启(每日急停次数≤3 次),防止胶料在胶管内积压固化(固化后需拆解清理,耗时 2-4 小时)。对连续生产(>8 小时)的场景,每 2 小时需清洁胶嘴一次(用专用溶剂擦拭),防止胶料残留堵塞;每 4 小时检查一次胶料余量,余量<10% 时及时补胶(补胶时需避免混入空气)。环境因素也需控制:车间温度保持 15-30℃(低于 15℃时启动环境加热),相对湿度≤70%(高湿度会影响胶料固化速度),避免粉尘过多(需配备除尘装置,粉尘浓度≤10mg/m)污染胶面。
Real time monitoring and adjustment during operation are the core to ensure the quality of sealing. The operator needs to continuously observe the appearance of the glue line: the normal glue line should be smooth, without bubbles, and without missing glue. If bubbles (mixed with air) appear, the machine should be stopped to discharge the air inside the hose; If the glue line becomes thinner (insufficient glue amount), check whether the pressure of the glue pump has decreased (it needs to be maintained at 0.8-1.5MPa); If there are burrs (worn rubber nozzle), replace the rubber nozzle in a timely manner (replacement time<5 minutes). During equipment operation, it is necessary to avoid emergency stops and starts (with a daily emergency stop frequency of ≤ 3 times) to prevent the rubber material from accumulating and solidifying in the hose (after solidification, it needs to be disassembled and cleaned, which takes 2-4 hours). For continuous production (>8 hours) scenarios, the rubber nozzle needs to be cleaned every 2 hours (wiped with a special solvent) to prevent residual rubber material from clogging; Check the remaining amount of adhesive every 4 hours, and promptly replenish the adhesive when the remaining amount is less than 10% (avoid mixing air when replenishing the adhesive). Environmental factors also need to be controlled: the workshop temperature should be maintained at 15-30 ℃ (environmental heating should be started when it is below 15 ℃), the relative humidity should be ≤ 70% (high humidity will affect the curing speed of the rubber material), and excessive dust (dust removal device should be equipped, dust concentration ≤ 10mg/m) should be avoided from contaminating the rubber surface.
设备维护与保养直接影响使用寿命和运行稳定性。每日生产结束后,需彻底清洗胶路系统:用清洗溶剂(如异丙醇、专用清洗剂)冲洗胶泵、胶管、胶嘴,直至流出液体无残留胶料(清洗时间 10-15 分钟),防止胶料固化堵塞(未清洗时故障率增加 50%)。每周检查运动部件:导轨添加润滑脂(每米导轨用量 5-10g),轴承检查磨损(间隙>0.1mm 时更换),确保移动顺畅(无卡顿)。每月校准计量系统:通过称重法确认实际胶量与设定值的偏差(偏差≤±3%),必要时调整胶泵转速或压力;检查传感器精度(如位置传感器误差≤0.1mm),确保定位准确。长期停用(>7 天)时,需排空胶路内所有胶料,注入保护剂(防止氧化腐蚀),并关闭电源和气源,覆盖防尘罩。
Equipment maintenance and upkeep directly affect the service life and operational stability. After daily production, the rubber system needs to be thoroughly cleaned: rinse the rubber pump, hose, and nozzle with cleaning solvents (such as isopropanol, specialized cleaning agents) until there is no residual rubber material flowing out (cleaning time 10-15 minutes), to prevent the rubber material from solidifying and blocking (failure rate increases by 50% when not cleaned). Weekly inspection of moving parts: add lubricating grease to the guide rail (5-10g per meter of guide rail), check for bearing wear (replace when clearance>0.1mm), ensure smooth movement (no jamming). Monthly calibration of the measuring system: Confirm the deviation between the actual glue amount and the set value through weighing method (deviation ≤± 3%), and adjust the glue pump speed or pressure if necessary; Check the accuracy of the sensor (such as position sensor error ≤ 0.1mm) to ensure accurate positioning. When it is not used for a long time (>7 days), all rubber materials in the rubber path should be emptied, protective agents should be injected (to prevent oxidation and corrosion), and the power and gas sources should be turned off, and a dust cover should be covered.
安全操作规范是避免事故的前提。设备运行时,操作人员需与运动部件保持安全距离(≥500mm),禁止用手接触胶嘴或工件(防止夹伤或烫伤,胶料温度可能达 50℃)。胶料和清洗剂多为易燃物,车间需禁止明火,并配备灭火器(每 50㎡至少 1 具);溶剂挥发气体需通过排风系统排出(风量≥10 次 / 小时),浓度控制在爆炸下限的 25% 以下。设备接地电阻需≤4Ω(防止静电火花),电气系统需定期检查绝缘(绝缘电阻≥1MΩ),避免漏电事故。此外,操作人员需经培训合格后方可上岗,熟悉紧急停机按钮位置(响应时间<1 秒),确保突发情况时能快速停机。
Safe operating procedures are a prerequisite for avoiding accidents. During equipment operation, operators must maintain a safe distance (≥ 500mm) from moving parts and are prohibited from touching the rubber nozzle or workpiece with their hands (to prevent pinching or scalding, as the temperature of the rubber material may reach 50 ℃). Rubber and cleaning agents are mostly flammable materials, and open flames are prohibited in the workshop, and fire extinguishers (at least one per 50 square meters) should be equipped; The solvent volatile gas needs to be discharged through the exhaust system (air volume ≥ 10 times/hour), and the concentration should be controlled below 25% of the lower explosive limit. The grounding resistance of the equipment should be ≤ 4 Ω (to prevent static sparks), and the insulation of the electrical system should be regularly checked (insulation resistance ≥ 1M Ω) to avoid leakage accidents. In addition, operators must be trained and qualified before taking up their posts, familiar with the position of the emergency stop button (response time<1 second), and ensure that they can quickly stop the machine in case of emergencies.
本文由双组份打胶机友情奉献.更多有关的知识请点击:http://www.jncsjx.com我们将会对您提出的疑问进行详细的解答,欢迎您登录网站留言.
This article is a friendly contribution from glass coating machine equipment For more information, please click: http://www.jncsjx.com We will provide detailed answers to your questions. You are welcome to log in to our website and leave a message
- 卧式丁基胶涂布机:选型需考量这些方面 2025/07/25
- 全自动封胶线使用注意事项:保障高效稳定运行的关键要点 2025/07/24
- 双组份打胶机怎么用?使用方法解析 2025/07/23
- 全自动封胶线胶线的关键特性与应用要点 2025/07/22
- 中空玻璃加工设备的组成解析:从切割到密封 2025/07/21
- 全自动封胶线是什么的相关介绍 2025/07/18
- 中空玻璃加工设备主要类型及用途 2025/07/16
- 卧式丁基胶涂布机操作技术规范 2025/07/14
- 双组份打胶机如何减少堵塞问题 2025/07/11
- 告别繁琐涂胶,立式丁基胶涂布机让效率与精度双赢 2025/07/10