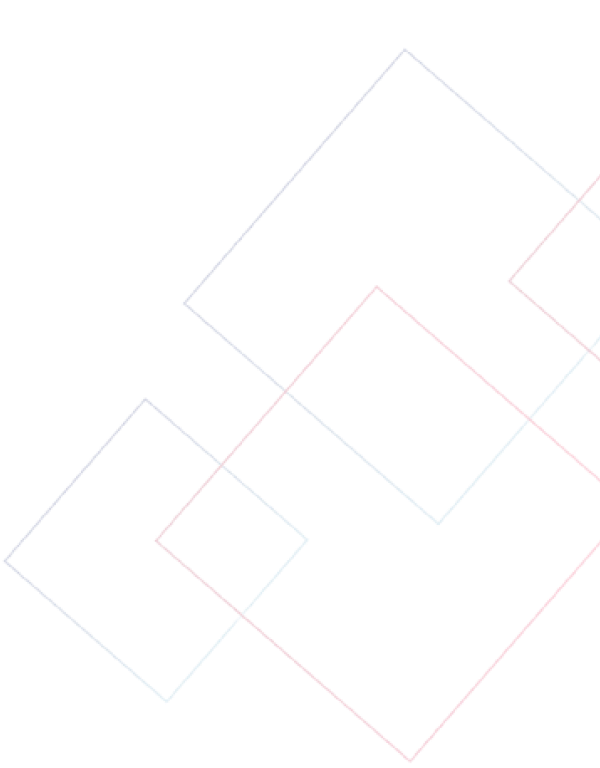
双组份打胶机如何减少堵塞问题
时间:2025-07-11 来源:http://www.jncsjx.com/ 发布人:昌盛机械
双组份打胶机的堵塞问题多源于胶料混合不均、杂质混入或设备部件残留,通过规范操作流程、优化维护方式,可有效降低堵塞概率,保障打胶作业的连续性。
The clogging problem of two-component gluing machines is mainly caused by uneven mixing of rubber materials, impurities, or residual equipment components. By standardizing operating procedures and optimizing maintenance methods, the probability of clogging can be effectively reduced to ensure the continuity of gluing operations.
胶料预处理环节是减少堵塞的基础。双组份胶料(如 A 胶和 B 胶)在使用前需进行充分搅拌,避免因沉淀导致的成分不均 —— 若胶料中存在未分散的颗粒,易在管路或混合腔中形成堆积,逐渐造成堵塞。对于粘度较高的胶料,可在使用前进行预热(温度控制在胶料说明书建议范围内),降低流动性阻力,减少在管路内的滞留。同时,需过滤胶料中的杂质,通过在胶料桶出口加装滤网(目数根据胶料颗粒度选择,通常为 80-120 目),拦截生产过程中可能混入的灰尘、金属碎屑等异物,从源头切断堵塞物的来源。
The pre-treatment process of rubber material is the foundation for reducing blockage. Two component adhesive materials (such as A and B adhesives) need to be thoroughly stirred before use to avoid uneven composition caused by precipitation - if there are undissolved particles in the adhesive material, they can easily accumulate in the pipeline or mixing chamber, gradually causing blockage. For adhesive materials with high viscosity, preheating (temperature control within the recommended range in the adhesive material manual) can be carried out before use to reduce flow resistance and minimize retention in the pipeline. At the same time, impurities in the rubber material need to be filtered by installing a filter screen at the outlet of the rubber material barrel (the mesh size is selected according to the particle size of the rubber material, usually 80-120 mesh) to intercept foreign objects such as dust and metal debris that may be mixed in during the production process, and cut off the source of blockages from the source.
设备参数的精准设置能减少胶料残留堵塞。混合比例失调是常见诱因,若 A、B 胶的配比偏差超过 5%,可能导致胶料在混合腔中反应不完全,产生固化颗粒。需定期校准计量泵的输出精度,通过称重法检测单位时间内的出胶量,确保配比误差控制在允许范围。出胶压力和速度也需匹配胶料特性,压力过高易导致胶料在管路内过度挤压形成沉淀,速度过快则可能使胶料在混合腔中混合不充分,建议根据胶料粘度逐步调试参数,以出胶顺畅、无明显飞溅为宜。此外,每次停机前需执行 “清洗程序”,通过专用清洗液(如溶剂型胶料用专用稀释剂)冲洗混合腔和出胶嘴,将残留胶料彻底排出。
Accurate setting of equipment parameters can reduce residual blockage of rubber materials. Mixing ratio imbalance is a common cause. If the ratio deviation of A and B adhesives exceeds 5%, it may lead to incomplete reaction of the adhesive in the mixing chamber, resulting in solidified particles. The output accuracy of the metering pump needs to be calibrated regularly, and the glue output per unit time should be detected by weighing method to ensure that the proportioning error is controlled within the allowable range. The dispensing pressure and speed also need to match the characteristics of the adhesive material. Excessive pressure can easily cause the adhesive material to be excessively squeezed and precipitate in the pipeline, while excessive speed may result in insufficient mixing of the adhesive material in the mixing chamber. It is recommended to gradually adjust the parameters according to the viscosity of the adhesive material to ensure smooth dispensing without obvious splashing. In addition, before each shutdown, a "cleaning procedure" must be performed to thoroughly flush the mixing chamber and dispensing nozzle with a specialized cleaning solution (such as a solvent based adhesive diluent) to remove any residual adhesive.
管路与部件的定期维护是防堵塞的关键。管路内壁若积累胶垢,会缩小流通截面,增加堵塞风险,需每周拆解管路进行清洗 —— 对于软管,可采用高压气流冲洗内壁;金属硬管则可用专用通条清理附着的胶层。混合腔和静态混合器是堵塞高发区,其内部的螺旋叶片易缠绕残留胶料,需每日作业结束后拆卸清洗,必要时用软毛刷清理叶片间隙。出胶嘴的口径需与胶料粘度匹配,粘度高的胶料应选用较大口径的喷嘴,避免因流速过慢导致胶料在出口处固化,同时需每日检查喷嘴是否有胶料残留,发现结晶或硬块及时用专用工具清理。
Regular maintenance of pipelines and components is key to preventing blockages. If adhesive deposits accumulate on the inner wall of the pipeline, it will reduce the flow cross-section and increase the risk of blockage. It is necessary to disassemble the pipeline for cleaning every week - for hoses, high-pressure airflow can be used to flush the inner wall; Metal hard pipes can be cleaned of the attached adhesive layer using dedicated strips. The mixing chamber and static mixer are high-risk areas for blockage, and the spiral blades inside are prone to entanglement with residual rubber material. They need to be disassembled and cleaned after daily work, and if necessary, the blade gaps should be cleaned with a soft bristled brush. The diameter of the dispensing nozzle should match the viscosity of the adhesive material. For adhesive materials with high viscosity, larger diameter nozzles should be used to avoid solidification of the adhesive material at the outlet due to slow flow rate. At the same time, the nozzle should be checked daily for any residue of adhesive material, and if crystals or hard blocks are found, they should be cleaned with specialized tools in a timely manner.
环境与储存条件的控制不可忽视。胶料储存需密封良好,避免空气进入形成结皮 —— 结皮的胶块若混入打胶系统,会直接造成管路堵塞。储存环境的温湿度需符合胶料要求,高温高湿易导致胶料提前反应,生成固化颗粒,建议将胶料存放于阴凉干燥处,并遵循 “先进先出” 原则,避免过期胶料投入使用。作业环境需保持清洁,定期清理工作台面的胶料残渣,防止其被意外带入胶料桶或进料口,同时在设备进料口加装防尘盖,减少空气中的灰尘混入胶料。
The control of environment and storage conditions cannot be ignored. The storage of rubber materials should be well sealed to prevent air from entering and forming a crust - if the crust rubber blocks mix into the gluing system, it will directly cause pipeline blockage. The temperature and humidity of the storage environment should meet the requirements of the adhesive material. High temperature and humidity can easily cause the adhesive material to react prematurely and form solidified particles. It is recommended to store the adhesive material in a cool and dry place, and follow the "first in, first out" principle to avoid using expired adhesive material. The working environment needs to be kept clean, and the residue of adhesive on the workbench should be regularly cleaned to prevent it from being accidentally brought into the adhesive bucket or feeding port. At the same time, a dust cover should be installed at the equipment feeding port to reduce the mixing of dust in the air into the adhesive.
操作规范的严格执行能从流程上规避堵塞。换胶时需彻底排空管路内的残留胶料,避免新旧胶料混合产生化学反应(部分不同批次胶料可能存在成分差异),形成难以清除的硬块。长时间停机前,需用清洗液冲洗整个打胶系统,确保管路、混合腔和喷嘴内无胶料残留,防止停机期间胶料固化堵塞。操作人员需定时巡检设备运行状态,观察出胶是否顺畅、胶条是否均匀,若发现出胶量突然减少或压力异常升高,需立即停机检查,避免小堵塞发展为严重故障。
The strict implementation of operational standards can avoid blockages in the process. When changing the glue, it is necessary to thoroughly drain the residual glue in the pipeline to avoid chemical reactions caused by the mixing of new and old glue (some different batches of glue may have compositional differences), which can form hard lumps that are difficult to remove. Before a prolonged shutdown, it is necessary to rinse the entire gluing system with cleaning solution to ensure that there is no residue of glue in the pipelines, mixing chambers, and nozzles, in order to prevent the glue from solidifying and blocking during the shutdown period. Operators need to regularly inspect the operation status of the equipment, observe whether the glue is smooth and whether the glue strip is uniform. If a sudden decrease in glue output or an abnormal increase in pressure is found, the machine should be stopped immediately for inspection to avoid small blockages from developing into serious faults.
本文由双组份打胶机友情奉献.更多有关的知识请点击:http://www.jncsjx.com我们将会对您提出的疑问进行详细的解答,欢迎您登录网站留言.
This article is a friendly contribution from glass coating machine equipment For more information, please click: http://www.jncsjx.com We will provide detailed answers to your questions. You are welcome to log in to our website and leave a message
- 中空玻璃生产线:一条中空线至少需要几个人? 2025/08/23
- 中空玻璃生产线的性能特点 2025/08/23
- 中空玻璃生产线安装操作要注意什么? 2025/08/17
- 中空玻璃填充氩气的作用 2025/08/16
- 胶条式和铝条式中空玻璃的组装区别 2025/08/12
- 玻璃清洗机使用过程中常见问题、注意事项及维护保养相关知识 2025/08/09
- 中空玻璃设备清洗机的维护保养工作有哪些 2025/08/09
- 中空玻璃的基本制造工艺流程是什么? 2025/08/01
- 双组份打胶机详解:从设计到使用维护 2025/07/30
- 双组份打胶机:应用领域与核心优势 2025/07/28