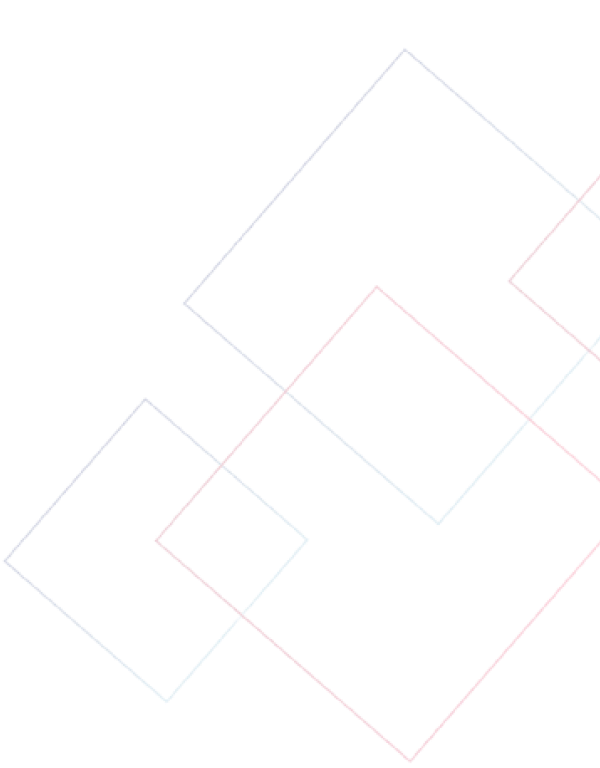
中空玻璃生产线:从原料到成品的 “规范通关秘籍”
时间:2025-06-24 来源:http://www.jncsjx.com/ 发布人:昌盛机械
在建筑节能与采光需求日益增长的当下,中空玻璃凭借优异的隔热隔音性能成为市场 “宠儿”。而中空玻璃生产线如同精密的 “玻璃智造工厂”,从原片切割到密封合片,每一步操作都关乎产品质量。想要驾驭这条生产线,必须严格遵循操作规范,才能确保产出高品质的中空玻璃。
In the current era of increasing demand for building energy efficiency and lighting, insulated glass has become the "darling" of the market due to its excellent thermal and sound insulation performance. The production line of insulating glass is like a precision "glass intelligent manufacturing factory", from cutting raw sheets to sealing and laminating, every step of the operation is related to product quality. To operate this production line, it is necessary to strictly follow the operating procedures to ensure the production of high-quality insulated glass.
开机前:筑牢安全与准备的 “双重防线”
Before startup: Build a "dual defense line" of safety and preparation
启动生产线前,安全检查与设备调试缺一不可。首先,操作人员需穿戴好防护装备,包括安全帽、防护手套与护目镜,避免玻璃碎屑划伤或机械部件意外碰撞。其次,对生产线各环节进行全面 “体检”:检查传输辊道是否运转顺畅,确保无卡顿、异响;确认清洗干燥机的毛刷、风机与加热装置功能正常,避免因清洗不净或干燥不充分影响后续工序;检查密封胶涂布机的胶管是否堵塞、计量泵压力是否稳定,防止胶量不均导致密封失效。同时,还需检查电控系统的线路连接与仪表参数,确保设备运行参数处于安全范围。此外,备好足量的干燥剂、密封胶、间隔条等耗材,并确认其质量符合生产标准,为生产做好充足准备。
Before starting the production line, safety checks and equipment debugging are indispensable. Firstly, operators need to wear protective equipment, including helmets, gloves, and goggles, to avoid scratches from glass shards or accidental collisions with mechanical components. Secondly, conduct a comprehensive "physical examination" of each link of the production line: check whether the conveyor roller is running smoothly, ensuring no jamming or abnormal noise; Confirm that the brushes, fans, and heating devices of the cleaning and drying machine are functioning properly to avoid affecting subsequent processes due to incomplete cleaning or drying; Check if the rubber hose of the sealant coating machine is blocked and if the pressure of the metering pump is stable to prevent uneven adhesive volume from causing seal failure. At the same time, it is necessary to check the wiring connections and instrument parameters of the electronic control system to ensure that the operating parameters of the equipment are within a safe range. In addition, prepare sufficient desiccants, sealants, spacer strips and other consumables, and confirm that their quality meets production standards to make adequate preparations for production.
原片切割:尺寸精准的 “玻璃裁剪术”
Original cutting: precise size "glass cutting technique"
原片切割是生产的首道关键工序。根据订单要求,操作人员需在控制系统中准确输入玻璃的尺寸与数量,确保切割精度控制在 ±0.5 毫米以内。切割时,应匀速推进玻璃原片,避免因速度过快导致切割面不平整或崩边;同时观察切割刀轮的磨损情况,若发现刀痕变宽、玻璃边缘出现锯齿状,需及时更换刀轮,保证切割质量。切割后的玻璃需轻拿轻放,避免碰撞产生暗伤,并按尺寸分类存放,便于后续工序取用。此外,定期清理切割机台面与废料收集装置,防止碎屑堆积影响设备运行。
Original cutting is the first critical process in production. According to the order requirements, the operator needs to accurately input the size and quantity of the glass in the control system to ensure that the cutting accuracy is controlled within ± 0.5 millimeters. When cutting, the glass sheet should be pushed at a constant speed to avoid uneven cutting surfaces or broken edges due to excessive speed; At the same time, observe the wear of the cutting wheel. If the knife marks become wider or the glass edges show jagged edges, the cutting wheel should be replaced in a timely manner to ensure cutting quality. The cut glass should be handled gently to avoid collision and hidden damage, and stored according to size for easy access in subsequent processes. In addition, regularly clean the cutting machine table and waste collection device to prevent debris accumulation from affecting equipment operation.
清洗干燥:打造洁净表面的 “关键战役”
Cleaning and drying: the 'key battle' for creating clean surfaces
清洗干燥环节直接影响中空玻璃的密封效果与使用寿命。将切割好的玻璃片平稳放置在传输辊道上,确保玻璃与辊道贴合紧密,避免传输过程中偏移或滑落。清洗机通过毛刷与高压水流去除玻璃表面的灰尘、油污,操作人员需监控清洗液的浓度与污浊程度,当清洗液变浑浊或 pH 值超出正常范围时,及时更换新液。清洗后的玻璃进入干燥区,利用热风或红外加热装置快速蒸发水分,此时需关注干燥温度与时间:温度过低或时间过短会导致水分残留,影响密封胶的粘结力;温度过高则可能使玻璃表面产生热应力。干燥后的玻璃应立即转入下一工序,避免长时间暴露在空气中二次吸附灰尘。
The cleaning and drying process directly affects the sealing effect and service life of insulated glass. Place the cut glass pieces steadily on the conveyor roller to ensure a tight fit between the glass and the roller, avoiding displacement or slipping during transportation. The cleaning machine uses a brush and high-pressure water flow to remove dust and oil stains from the glass surface. The operator needs to monitor the concentration and degree of contamination of the cleaning solution. When the cleaning solution becomes turbid or the pH value exceeds the normal range, it should be replaced with a new solution in a timely manner. After cleaning, the glass enters the drying area and quickly evaporates moisture using hot air or infrared heating devices. At this time, attention should be paid to the drying temperature and time: too low a temperature or too short a time can cause residual moisture, affecting the bonding strength of the sealant; If the temperature is too high, it may cause thermal stress on the surface of the glass. The dried glass should be immediately transferred to the next process to avoid prolonged exposure to air for secondary dust adsorption.
间隔框制作与填充:构筑保温隔音的 “隐形骨架”
Interval frame production and filling: constructing an "invisible skeleton" for insulation and sound insulation
间隔框的制作与填充决定了中空玻璃的隔热性能。根据玻璃规格,使用弯角机或切割机将铝间隔条加工成相应尺寸的矩形框,拼接处需保证严丝合缝,防止漏气影响中空层的密封效果。间隔框制作完成后,需填充足量的干燥剂,干燥剂应具有良好的吸附性能,能有效吸收中空层内的水分,避免玻璃内部起雾。填充时需控制干燥剂的填充量,过少无法达到吸湿效果,过多则可能导致间隔框变形。填充完毕后,及时封闭间隔框两端的开口,防止干燥剂散落或受潮失效。
The production and filling of spacer frames determine the thermal insulation performance of insulating glass. According to the glass specifications, use a corner bending machine or cutting machine to process the aluminum spacer into rectangular frames of corresponding sizes, and ensure that the joints are tightly sealed to prevent air leakage from affecting the sealing effect of the hollow layer. After the completion of the spacer frame production, a sufficient amount of desiccant should be filled. The desiccant should have good adsorption performance and be able to effectively absorb the moisture inside the hollow layer, avoiding fogging inside the glass. When filling, it is necessary to control the amount of desiccant filling. Too little cannot achieve the moisture absorption effect, and too much may cause deformation of the spacer frame. After filling, promptly seal the openings at both ends of the spacer to prevent the desiccant from scattering or becoming ineffective due to moisture.
合片与密封:锁住性能的 “终极封印”
Splicing and Sealing: The Ultimate Seal for Locking Performance
合片是将两片玻璃与间隔框组合成中空结构的关键步骤。操作人员需双手平稳托起玻璃,将间隔框居中放置在下层玻璃表面,确保四个边角对齐,再将上层玻璃精准覆盖。合片过程中避免手指直接接触玻璃内表面,防止留下指纹或污渍影响美观与性能。合片完成后,立即进行密封处理,先在间隔框两侧均匀涂布第一道丁基胶,形成初始密封层;随后通过双组份打胶机在玻璃四周涂布硅酮密封胶或聚硫密封胶,涂布时需控制胶层厚度与宽度,保证密封胶与玻璃、间隔框充分粘结。打胶完成后的中空玻璃需静置固化,固化期间避免移动或震动,确保密封胶完全干燥,形成牢固的密封结构。
Splicing is a key step in combining two pieces of glass with a spacer frame to form a hollow structure. The operator needs to steadily lift the glass with both hands, place the spacer frame in the center on the surface of the lower glass, ensure that the four corners are aligned, and then accurately cover the upper glass. During the lamination process, avoid direct contact between fingers and the inner surface of the glass to prevent fingerprints or stains from affecting its appearance and performance. After the lamination is completed, immediately perform sealing treatment by evenly applying the first layer of butyl rubber on both sides of the spacer frame to form the initial sealing layer; Subsequently, a two-component glue machine is used to apply silicone sealant or polysulfide sealant around the glass. During the application process, the thickness and width of the adhesive layer should be controlled to ensure that the sealant is fully bonded to the glass and spacer frame. After the completion of gluing, the insulated glass needs to be left to cure. During the curing period, avoid moving or shaking to ensure that the sealant is completely dry and forms a firm sealing structure.
收尾与维护:保障生产线的 “持久战力”
Closing and Maintenance: Ensuring the 'Enduring Strength' of the Production Line
每日生产结束后,操作人员需对生产线进行全面清理与维护。清除设备表面与传输辊道上的玻璃碎屑、胶渍等杂物,避免其进入机械部件影响运行;对切割刀轮、毛刷辊、胶嘴等易损件进行检查与保养,及时更换磨损严重的部件;同时,检查各润滑点的润滑油量,不足时及时补充。此外,还需对电控系统进行常规检查,确保线路无松动、仪表显示正常。定期对生产线进行精度校准与性能测试,如检查切割尺寸误差、密封胶涂布均匀性等,发现问题及时调整,保障生产线持续稳定运行。
After daily production, operators need to conduct a comprehensive cleaning and maintenance of the production line. Remove glass debris, adhesive stains, and other debris from the surface of the equipment and the conveyor roller to prevent them from entering mechanical components and affecting operation; Inspect and maintain vulnerable parts such as cutting blade wheels, brush rollers, and rubber nozzles, and replace severely worn parts in a timely manner; At the same time, check the amount of lubricating oil at each lubrication point and replenish it promptly if it is insufficient. In addition, routine inspections of the electronic control system are required to ensure that the wiring is not loose and the instrument display is normal. Regularly perform precision calibration and performance testing on the production line, such as checking cutting size errors, sealant coating uniformity, etc. Any problems found should be adjusted in a timely manner to ensure the continuous and stable operation of the production line.
本文由中空玻璃生产线友情奉献.更多有关的知识请点击:http://www.jncsjx.com我们将会对您提出的疑问进行详细的解答,欢迎您登录网站留言.
This article is a friendly contribution from glass coating machine equipment For more information, please click: http://www.jncsjx.com We will provide detailed answers to your questions. You are welcome to log in to our website and leave a message
- 双组份打胶机:双组分打胶与单组份打胶的简介及注意事项 2025/08/30
- 双组份打胶机:中空玻璃自动打胶机的调整与操作 2025/08/30
- 中空玻璃打胶机的调试方法你会了吗? 2025/08/24
- 中空玻璃生产线:一条中空线至少需要几个人? 2025/08/23
- 中空玻璃生产线的性能特点 2025/08/23
- 中空玻璃生产线安装操作要注意什么? 2025/08/17
- 中空玻璃填充氩气的作用 2025/08/16
- 胶条式和铝条式中空玻璃的组装区别 2025/08/12
- 玻璃清洗机使用过程中常见问题、注意事项及维护保养相关知识 2025/08/09
- 中空玻璃设备清洗机的维护保养工作有哪些 2025/08/09