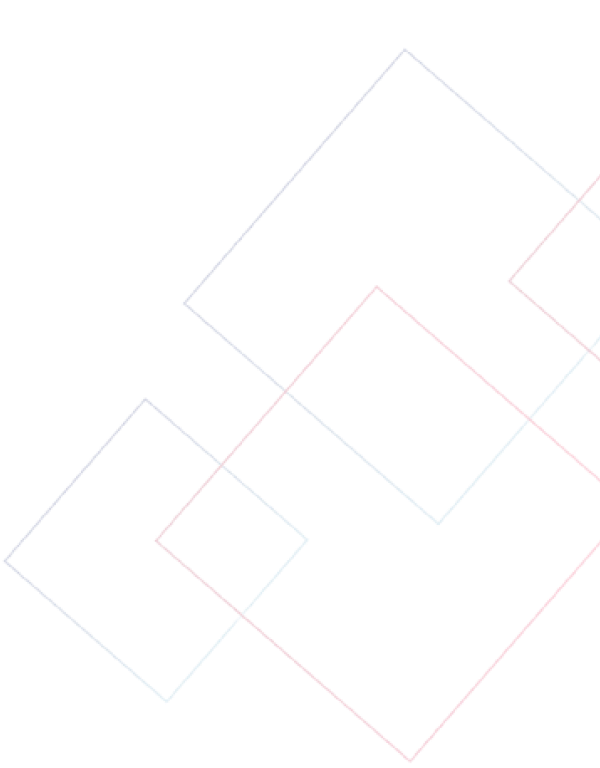
中空玻璃加工设备:解密 “空气夹层” 的诞生工厂
时间:2025-07-04 来源:http://www.jncsjx.com/ 发布人:昌盛机械
在建筑节能与工业玻璃制造领域,中空玻璃凭借两层玻璃间的空气夹层(通常 6-20mm),成为隔绝噪音、减少热量传递的 “全能选手”。而这层看似简单的 “空气屏障”,实则需要一整条精密设备链的协同运作。从玻璃原片的 “精准剪裁” 到密封胶的 “无缝拥抱”,中空玻璃加工设备如同一位隐形的 “空间编织者”,用机械臂的舞动与传感器的 “眼睛”,将普通玻璃转化为兼具功能性与美观性的复合产品。
In the fields of building energy efficiency and industrial glass manufacturing, insulated glass has become an all-around player in isolating noise and reducing heat transfer with the air interlayer between two layers of glass (usually 6-20mm). And this seemingly simple 'air barrier' actually requires the coordinated operation of a whole chain of precision equipment. From precise cutting of glass raw sheets to seamless embrace of sealants, insulated glass processing equipment is like an invisible "space weaver", using the movement of robotic arms and the "eyes" of sensors to transform ordinary glass into composite products that combine functionality and aesthetics.
原片玻璃的 “量体裁衣” 系统
The 'tailor-made' system for original glass sheets
加工的起点是对玻璃原片的尺寸处理,这需要切割机与磨边机的默契配合。切割机的核心是可高速旋转的金刚石刀头(硬度达莫氏 10 级),通过伺服电机控制其在玻璃表面划出深度 0.3-0.5mm 的轨迹,配合真空吸附式工作台(吸力达 80kPa)固定原片,确保切割尺寸误差≤0.1mm。切割后的玻璃边缘锋利如刃,磨边机的砂轮组(通常由粗砂轮、精砂轮、抛光轮三级组成)开始工作:粗砂轮(粒度 80-120 目)快速打磨出 45° 倒角,精砂轮(粒度 200-300 目)将边缘粗糙度降至 Ra≤1.6μm,最后抛光轮(羊毛毡 + 抛光膏)赋予边缘镜面效果,避免应力集中导致的玻璃自爆。整个过程中,红外对中传感器(精度 ±0.2mm)实时监测玻璃位置,确保边缘处理均匀一致。
The starting point of processing is the size treatment of the glass raw sheet, which requires the tacit cooperation between the cutting machine and the edging machine. The core of the cutting machine is a high-speed rotating diamond blade (with a hardness of 10 on the Mohs scale), which is controlled by a servo motor to draw a trajectory with a depth of 0.3-0.5mm on the glass surface. It is fixed with a vacuum adsorption worktable (with a suction force of 80kPa) to ensure that the cutting size error is ≤ 0.1mm. The edge of the cut glass is as sharp as a blade. The grinding wheel group of the edge grinder (usually composed of three stages: coarse grinding wheel, fine grinding wheel, and polishing wheel) starts working: the coarse grinding wheel (with a particle size of 80-120 mesh) quickly grinds out a 45 ° chamfer, the fine grinding wheel (with a particle size of 200-300 mesh) reduces the edge roughness to Ra ≤ 1.6 μ m, and finally the polishing wheel (wool felt+polishing paste) gives the edge a mirror effect to avoid stress concentration. Causing the glass to self destruct. Throughout the process, the infrared centering sensor (with an accuracy of ± 0.2mm) monitors the position of the glass in real-time to ensure uniform and consistent edge treatment.
洁净度的 “严苛守护者”
The 'strict guardian' of cleanliness
玻璃表面的尘埃、油渍会直接影响后续密封效果,清洗干燥设备承担着 “洁净把关” 的重任。清洗段采用多组对辊式毛刷(刷毛材质为尼龙 66,硬度邵氏 85A),以 1500rpm 的转速配合去离子水(电导率≤10μS/cm)冲刷玻璃表面,毛刷压力控制在 0.5-1.0N/cm?,既去除顽固污渍又不划伤玻璃。清洗后的玻璃进入烘干段,热风喷嘴以 80℃、20m/s 的气流吹扫表面(风速误差≤5%),配合底部红外加热板(温度均匀性 ±2℃),确保玻璃离开时表面含水率<0.1%。部分设备还配备静电消除器,通过电晕放电中和玻璃表面电荷(残留电压≤100V),避免吸附空气中的微尘。
Dust and oil stains on the surface of glass will directly affect the subsequent sealing effect, and cleaning and drying equipment bears the responsibility of "cleanliness control". The cleaning section uses multiple sets of roller type brushes (bristles made of nylon 66 with a hardness of 85A on the Shore scale) to wash the glass surface at a speed of 1500rpm with deionized water (conductivity ≤ 10 μ S/cm). The brush pressure is controlled between 0.5-1.0N/cm? Remove stubborn stains without scratching the glass. The cleaned glass enters the drying section, and the hot air nozzle blows the surface with an airflow of 80 ℃ and 20m/s (wind speed error ≤ 5%), combined with the bottom infrared heating plate (temperature uniformity ± 2 ℃), to ensure that the surface moisture content of the glass is less than 0.1% when it leaves. Some devices are also equipped with static eliminators, which neutralize the surface charges of the glass through corona discharge (residual voltage ≤ 100V), avoiding the adsorption of fine dust in the air.
间隔条的 “魔法塑形” 装置
The 'magic shaping' device of the spacer bar
中空玻璃的核心支撑是铝制间隔条,其加工需要折弯机与分子筛填充机的协同。折弯机的模具组(材质为 Cr12MoV,硬度 HRC58-62)可根据需求弯出矩形、圆形等不同形状,伺服电机驱动模具以 0.1mm 的精度控制折弯角度(误差≤0.5°),确保间隔条闭合时接口间隙<0.2mm。填充分子筛的过程如同给间隔条 “注入干燥剂”,真空填充机通过负压(压力≤10kPa)将直径 1-2mm 的球形分子筛(吸附量≥20% RH)吸入间隔条腔体,填充密度控制在 0.6-0.8g/cm?,既保证吸湿能力又避免过量导致间隔条变形。填充后,端部密封胶(丁基胶,黏度 1000-1500Pa?s)通过螺杆泵以 0.5mm 的厚度均匀涂布,将分子筛牢牢封存。
The core support of insulating glass is aluminum spacer bars, which require the cooperation of bending machines and molecular sieve filling machines for processing. The mold set of the bending machine (made of Cr12MoV material, hardness HRC58-62) can bend into different shapes such as rectangles and circles according to needs. The servo motor drives the mold to control the bending angle with an accuracy of 0.1mm (error ≤ 0.5 °), ensuring that the interface gap is less than 0.2mm when the spacer is closed. The process of filling the molecular sieve is like "injecting desiccant" into the spacer. The vacuum filling machine uses negative pressure (pressure ≤ 10kPa) to suck spherical molecular sieves with a diameter of 1-2mm (adsorption capacity ≥ 20% RH) into the spacer cavity, and the filling density is controlled at 0.6-0.8g/cm? Ensure moisture absorption capacity while avoiding excessive deformation of the spacer strip. After filling, the end sealant (butyl rubber, viscosity 1000-1500Pa? S) is evenly applied with a thickness of 0.5mm through a screw pump to firmly seal the molecular sieve.
合片与密封的 “精密对接” 环节
Precision docking link between lamination and sealing
两片处理好的玻璃需在合片设备上完成 “空气夹层” 的构建。真空吸附式合片机的上料臂(定位精度 ±0.3mm)将玻璃平稳放置在工作台,激光测距仪(精度 ±0.1mm)实时监测间隔条位置,确保两片玻璃的间距误差<0.5mm。对于 Low-E 玻璃等镀膜产品,设备自动识别膜面(通过光谱传感器检测反射率变化),避免镀膜面朝向错误影响节能效果。合片后的玻璃进入密封环节,双组份打胶机将丁基胶与硅酮胶分两次涂布:内层丁基胶(涂布速度 5-10m/min)形成第一道密封,隔绝空气渗透;外层硅酮胶(固化时间 24-48h)提供结构强度,胶层厚度控制在 8-12mm,通过压力传感器(精度 ±0.05MPa)确保胶量均匀,避免气泡或断胶。
Two pieces of processed glass need to be constructed with an "air interlayer" on the laminating equipment. The feeding arm of the vacuum adsorption laminating machine (positioning accuracy ± 0.3mm) smoothly places the glass on the workbench, and the laser rangefinder (accuracy ± 0.1mm) monitors the position of the spacer in real time to ensure that the distance error between the two pieces of glass is less than 0.5mm. For coated products such as Low-E glass, the equipment automatically identifies the film surface (detects changes in reflectivity through a spectral sensor), avoiding the influence of incorrect coating surface orientation on energy-saving effect. After the laminated glass enters the sealing process, the two-component glue machine applies butyl rubber and silicone rubber in two separate coats: the inner layer of butyl rubber (coating speed 5-10m/min) forms the first seal, isolating air infiltration; The outer layer of silicone adhesive (curing time 24-48 hours) provides structural strength, and the thickness of the adhesive layer is controlled at 8-12mm. The pressure sensor (accuracy ± 0.05MPa) ensures uniform adhesive volume and avoids bubbles or breakage.
本文由中空玻璃加工设备友情奉献.更多有关的知识请点击:http://www.jncsjx.com我们将会对您提出的疑问进行详细的解答,欢迎您登录网站留言.
This article is a friendly contribution from glass coating machine equipment For more information, please click: http://www.jncsjx.com We will provide detailed answers to your questions. You are welcome to log in to our website and leave a message
- 双组份打胶机:双组分打胶与单组份打胶的简介及注意事项 2025/08/30
- 双组份打胶机:中空玻璃自动打胶机的调整与操作 2025/08/30
- 中空玻璃打胶机的调试方法你会了吗? 2025/08/24
- 中空玻璃生产线:一条中空线至少需要几个人? 2025/08/23
- 中空玻璃生产线的性能特点 2025/08/23
- 中空玻璃生产线安装操作要注意什么? 2025/08/17
- 中空玻璃填充氩气的作用 2025/08/16
- 胶条式和铝条式中空玻璃的组装区别 2025/08/12
- 玻璃清洗机使用过程中常见问题、注意事项及维护保养相关知识 2025/08/09
- 中空玻璃设备清洗机的维护保养工作有哪些 2025/08/09